Electroplating process of vehicle parts
Classification of electroplating for vehicle parts
1. Decorative Coating
As a logo or decoration of a car, it is required to have a bright appearance after electroplating, a uniform and coordinated color tone, exquisite processing, and good corrosion resistance. Such as car signs, bumpers, wheel hubs, etc.
2. Protective Coating
Good corrosion resistance of parts is required, including zinc plating, cadmium plating, lead plating, zinc alloy, lead alloy.
3. Functional Coating
It is widely used, such as: tin plating, copper plating, lead-tin plating to improve the surface weld ability of parts; iron plating and chromium plating to repair the size of parts; silver plating to improve metal conductivity.
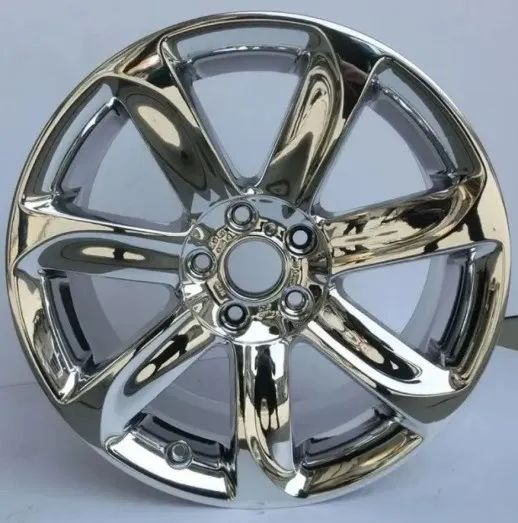
Specific electroplating process classification
1. Etching
Etching is a method of removing oxides and rust products on the surface of parts by using the dissolution and etching of acidic solutions. The characteristics of the automobile etching process include: the production pace is fast and the batch size is large.
2. Galvanized
Zinc coating is relatively stable in the air, has reliable protection ability for steel and low cost. Such as a medium-sized truck, the surface area of galvanized parts is 13-16m², accounting for more than 80% of the total plating area.
3. Copper or aluminum electroplating
Plastic product electroplating goes through roughening engraving work, the surface of the plastic material corrodes out microscopic pores, then electroplacting the aluminum in the surface.
Mainly used steel for automobiles is used as a basic decoration steel. The external mirror is bright, high-quality mirror, good corrosion resistance, and is mainly used for high-performance automobiles.
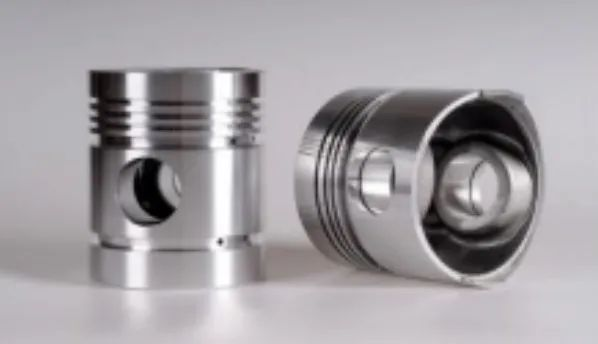
Post time: Nov-18-2022